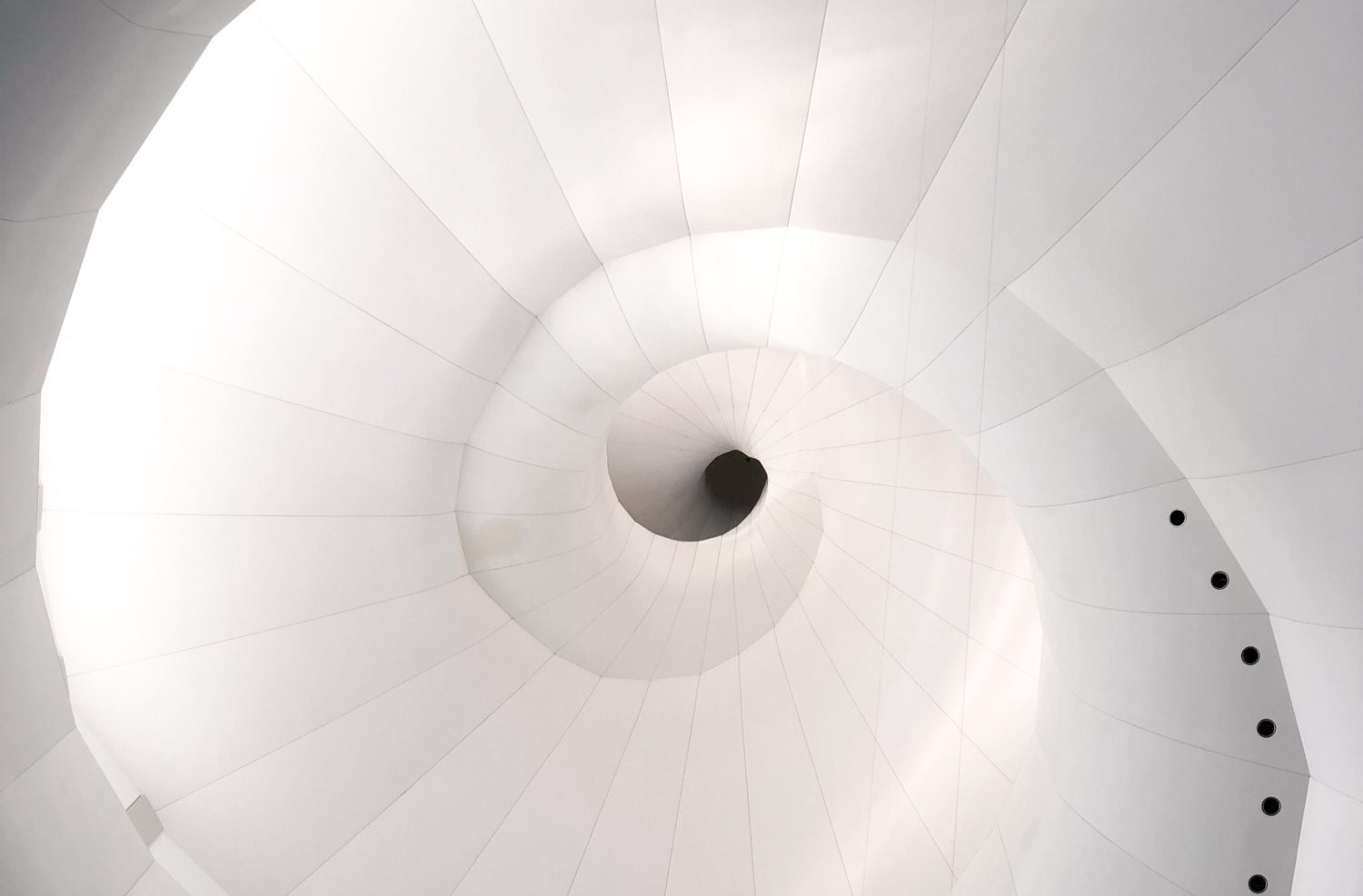
Biomimicry: How Nature's Design Inspires Engineering Advances in Micro and Nanotechnology
Nature has had millions of years to develop adaptations for living in harsh environments, and one of its most impressive achievements is the precise micro and nanoscale surface variations found in many organisms. These variations provide extraordinary benefits, such as the self-cleaning abilities of the lotus flower, antifouling properties of shark skin, and dry adhesion used by insects, lizards, and other animals.
Replicating Nature's Genius: Engineers and Scientists in Manufacturing Processes
Engineers and scientists have attempted to replicate properties of nature in manufacturing processes by creating a faithful copy of the nano and microstructure. However, while it’s possible to create specific microstructures in a lab and demonstrate their properties, they’re too small and fragile for industrial-scale use. To employ these functional structures on an industrial level, a rigid large tool must be manufactured to justify the cost.
Expanding the Active Area through UV Step and Repeat Technology
One way of expanding the active area of the structure is by employing UV step and repeat technology. This method requires making a sophisticated UV stamper and subsequently stamping the structure on UV curable resin. The process involves applying UV curable resin, pressing the stamper against the resin, curing the resin with UV light, separating the stamper from the cured resin, and repeating the steps at different positions. Modern UV step and repeat technology allows for recombination with high positioning accuracy, typically below 50 μm and over a size of 1×1 m².
-
This process can be simplified to the following steps:
- Application of UV curable resin
- Pressing the stamper against the resin
- Curing the resin with the UV light
- Separating stamper from cured resin
- Repeating the points 1 – 4 at different positions
However, the enlarged master produced using UV step and repeat technology is still not rigid enough for long-term use. This can be achieved by electroforming nickel shims. To further apply electroforming processes, the material must be conductive.
Â
This can be achieved by applying a thin metallic layer, such as chemical wet silvering or sputtering. Once the sample is conductive, it can be placed in an electroforming tank where nickel shims are manufactured. These nickel shims are solid and rigid tools for the subsequent production of large volumes of micro and/or nanostructures.