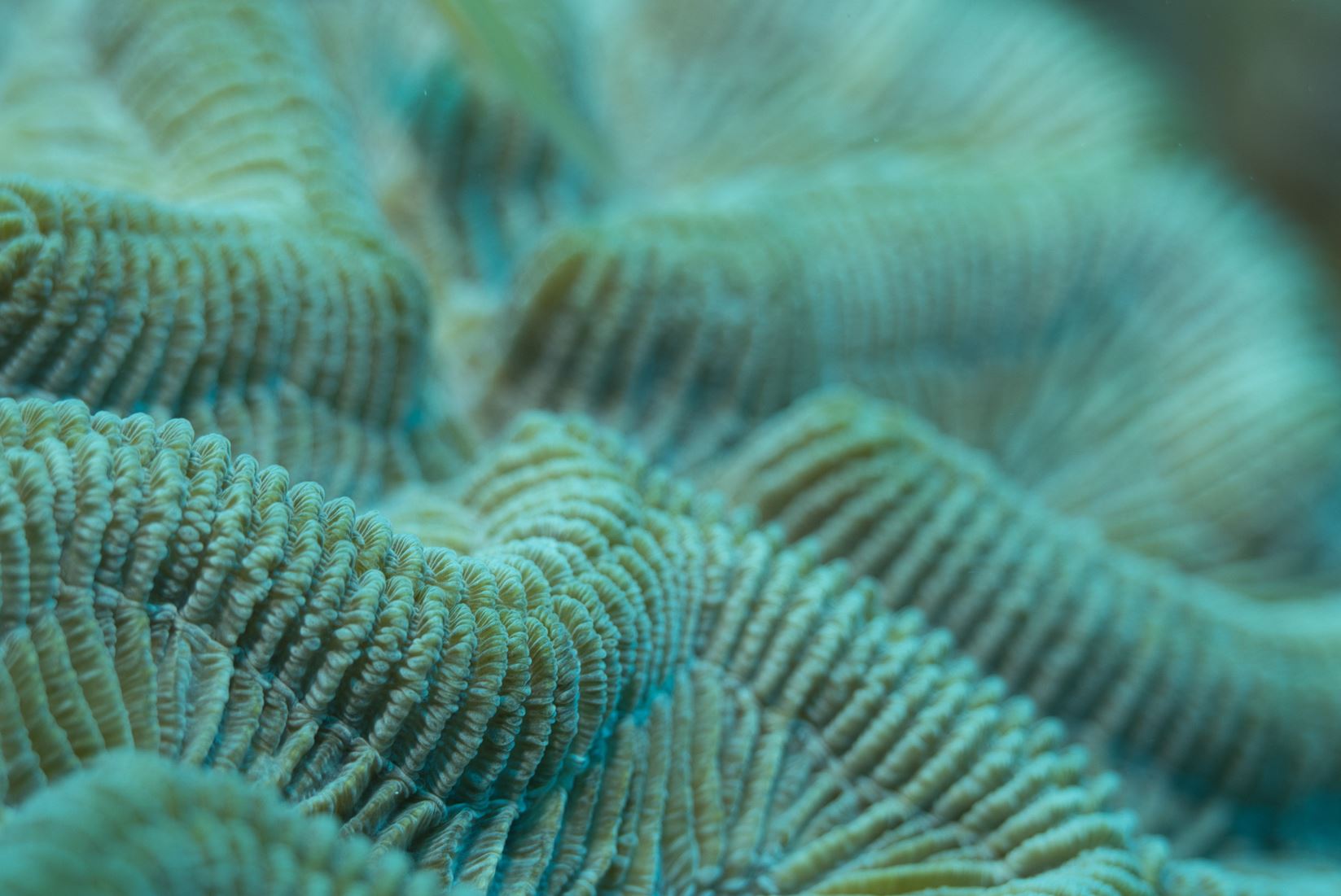
Biomimetics Evolution At The Micron Scale And Beyond
We would like to thank TTP.com and author Fred Hussain, for covering this relevant topic and highlighting so many interesting factors. The micro and nanotechnology team at 3D AG appreciates such on point content about biomimetics.
Harnessing Biomimicry: Inspiring Product and Industry Development
From Velcro to human flight, biomimicry has inspired the development of products and industries. During the 2020s, microfabrication and other bottom-up approaches will likely lead to many more bio-inspired ideas achieving technical and commercial success, says Fred Hussain.
Millions of years of evolution have created structures and materials with remarkable properties – and long inspired biomimicry. Human flight was inspired by the study of birds, and the tiny hooks on bur fruit prompted the development of Velcro – patented in 1955.
Now, microfabrication techniques alongside more specialised polymer processing, nanofabrication, electronics and materials science can produce smarter structures and solutions to many real-world problems. And going even smaller, approaches from nano and molecular biomimetics to those exploiting self-assembly will further enhance our ability to create structures and surfaces with improved properties.
In this blog, I give some examples of how microfabrication and other emerging technologies can be used to create new bio-inspired structures and materials:
-
Examples of Microfabrication
- Biomimicry by microfabrication
- Going smaller: biomimetics at the nano scale and beyond
Biomimicry by Microfabrication
Evolution has produced the most remarkable structures, shapes and colours to enhance the survival of plants and animals by reducing (or enhancing) properties such as drag, noise, adhesion, wear, fogging or the sheer strength-to-weight ratio of materials [1].
Meanwhile, on a more human timescale, microfabrication has moved beyond the semiconductor industry and is now widely used in digital printing, automotive, communications, display and biomedical industries, creating structures and materials with attractive properties alongside intelligence when used with electronics.
Combining these two different approaches – biomimetics and microfabrication – is an area receiving increased attention. I have been hugely inspired by using nature throughout my career in microfabrication, as shown by the following examples.
Superhydrophobic Structures or Coatings
Superhydrophobic structures and coatings have proven useful in applications ranging from anti-fog, anti-freeze, anti-corrosion, self-cleaning, anti-bacterial, microfluidics and oil–water separation. The lotus leaf has millions of microscopic hairs to stop water droplets from wetting out over the surface (see left image). We used SU8 fabricated polymer pillars (see right image) to give a similar super hydrophobic structure as the lotus leaf. Further potential exists in guiding fluid flow over these surfaces, by incorporating metal and insulating regions to make droplets travel in predetermined patterns under electrical control.
Adhesives
An interesting 2018 paper by Baik et. al. [2] discussed how microfabricated octopus suckers could potentially replace adhesives in both wet and dry skin patch applications. The authors developed a simple moulding process to produce biocompatible PDMS based tentacles and suckers. We have created an enhanced and more volume manufacturable version of this work at TTP (see right image).
Optical Arrays
Lens arrays inspired by the fly’s eye can be useful to create uniform irradiance distributions from non-uniform light sources, and such lenses can be easily and cheaply produced from hot embossed plastics. In addition, there are photo-patternable polymers such as Epo clad/core or Ormo clad/core, which guide light over a substrate surface, similar to optical fibres. Such technologies could be used to improve light collection on solar cells, head lamps or cameras.
Strength
Silicon is renowned as a strong and easily machinable material [3]. Its use alongside polyimide could rival or even surpass the strength-to-weight ratio of insect wings. At BAE SYSTEMS, I worked on Micro Air Vehicles (MAV) to mimic the dragonfly by using such materials and techniques (see right image). Today, many other lighter and stronger patternable materials, such as Graphene, CNTs, SU8 and hydrogels, are also available and could potentially produce superior results.
Drag Reduction
Silicon is renowned as a strong and easily machinable material [3]. Its use alongside polyimide could rival or even surpass the strength-to-weight ratio of insect wings. At BAE SYSTEMS, I worked on Micro Air Vehicles (MAV) to mimic the dragonfly by using such materials and techniques (see right image). Today, many other lighter and stronger patternable materials, such as Graphene, CNTs, SU8 and hydrogels, are also available and could potentially produce superior results.
Going Smaller: Biomimetics at the Nanoscale and Beyond
The basic properties and functions of biological systems are defined at the nanoscale. Both top-down (microfabrication and lithographic tools) and bottom-up (chemistry and biology) nanotechnologies are now being used to mimic such structures at the nano level, i.e. nano-biomimetics.
The remarkable adhesive properties of Gecko feet, for example, result from a very dense array of nano-fine hairs, called spatulae, interacting with surfaces through Van der Waal’s forces only. This has inspired gecko tape, which generates its stickiness using Kapton fibres, 0.2 micron in diameter and 2 micron long, made using a top-down process [5]. Tissue re-generation using nano-scale biomimetics produced in this way (nano fibres, scaffolds etc.) is another promising application area.
Going even smaller, molecular biomimetics is an emerging bottom-up field in which biotechnology is used to prepare functional molecules that can be integrated into nanotechnological devices [7]. For example, Genetically Engineered Proteins designed to bind to specific Inorganics (known as GEPIs) can be used in the assembly of functional nanostructures.
Another area where biology excels is self-assembly. In both living organisms and the lab, the principle is that appropriately designed and prepared nano-sized building blocks arrange themselves into complex, hierarchical structures for additional function. During his doctorate, my colleague Tianheng Zhao took inspiration from the costly natural opal, to create an artificial opal by causing self-assembly of spherical nanoparticles [8]. This produced a similar attractive iridescent visual appearance to the original at a fraction of the cost, thereby opening new applications in opto-electronics, energy storage, communications and sensing.
Summary
A lot can be learnt by closely studying nature. At the same time, the tools, processes and materials at our disposal are rapidly improving. We can therefore look to combine nature’s strategies of combinatorial building blocks and self-assembly along with advanced micro-, nano- and materials technology. This will likely lead many more bio-inspired ideas to technical and commercial success.
References
- Advances in Colloid and Interface Science
- Highly Adaptable and Biocompatible Octopus‐Like Adhesive Patches
- Silicon as a mechanical material
- AEROMEMS-II: A european research effort to develop MEMS based flow control technologies
- Gecko tape will stick you to ceiling, New Scientist
- Nano-Biomimetics for Nano/Micro Tissue Regeneration
- Molecular biomimetics: nanotechnology through biology, Nature.
- Bio-inspired Photonics